Prima dell’avvio della produzione di un qualunque dispositivo elettronico, la maggior parte delle aziende del mondo IT invia in Cina “eserciti” di ingegneri che passano settimane in remote fabbriche per limare o eliminare problematiche che potrebbero verificarsi in fase di fabbricazione, prima che i dispositivi arrivino nelle mani degli utenti.
Questo procedimento è costoso e faticoso e non esiste azienda in grado di avviare immediatamemte la produzione in massa di grandi quantità di dispositivi senza prima passare varie fasi preliminari di test.
Anna Shedletsky è un’ex dipendente di Apple e tra le fondatrici di Instrumental; insieme al suo collega Sam Weiss (anche lui ex dipendente Apple), ha passato mesi in Cina a risolvere problemi in fase di produzione dei prodotti della Mela, prima del loro lancio ufficiale. Questa startup nata quattro anni addietro – racconta CNBC – ha creato un particolre sistema di monitoraggio che prevede fotocamere nelle linee di assemblaggio, accoppiate a un software che sfrutta tecnologie di machine learning in grado di individuare vari difetti prima dell’avvio della produzione in grandi quantità.

Se l’idea di Instrumental prenderà piede, potrebbe permettere a molte aziende e startup di avviare la produzione di gadget vari negli stabilimenti asiatici, senza bisogno di avere a disposizione le risorse normalmente disponibili solo ai big dell’elettronica di consumo.
Tra i primi clienti di Instrumental, c’è Motorola – azienda sussidiaria di Lenovo – che ha cominciato a sfruttare questo sistema di controllo dall’inizio del 2018 per creare i suoi smartphone. “Anziché inviare eserciti di ingegneri sul posto, ognuno di questi può visualizzare dettagli dalle linee di assemblaggio in merito a ogni singola unità prodotta, direttamente dalle loro scrivanie a migliaia di chilometri di distanza”, spiega Kevin Zurawski, senior manufacturing manager di Motorola.
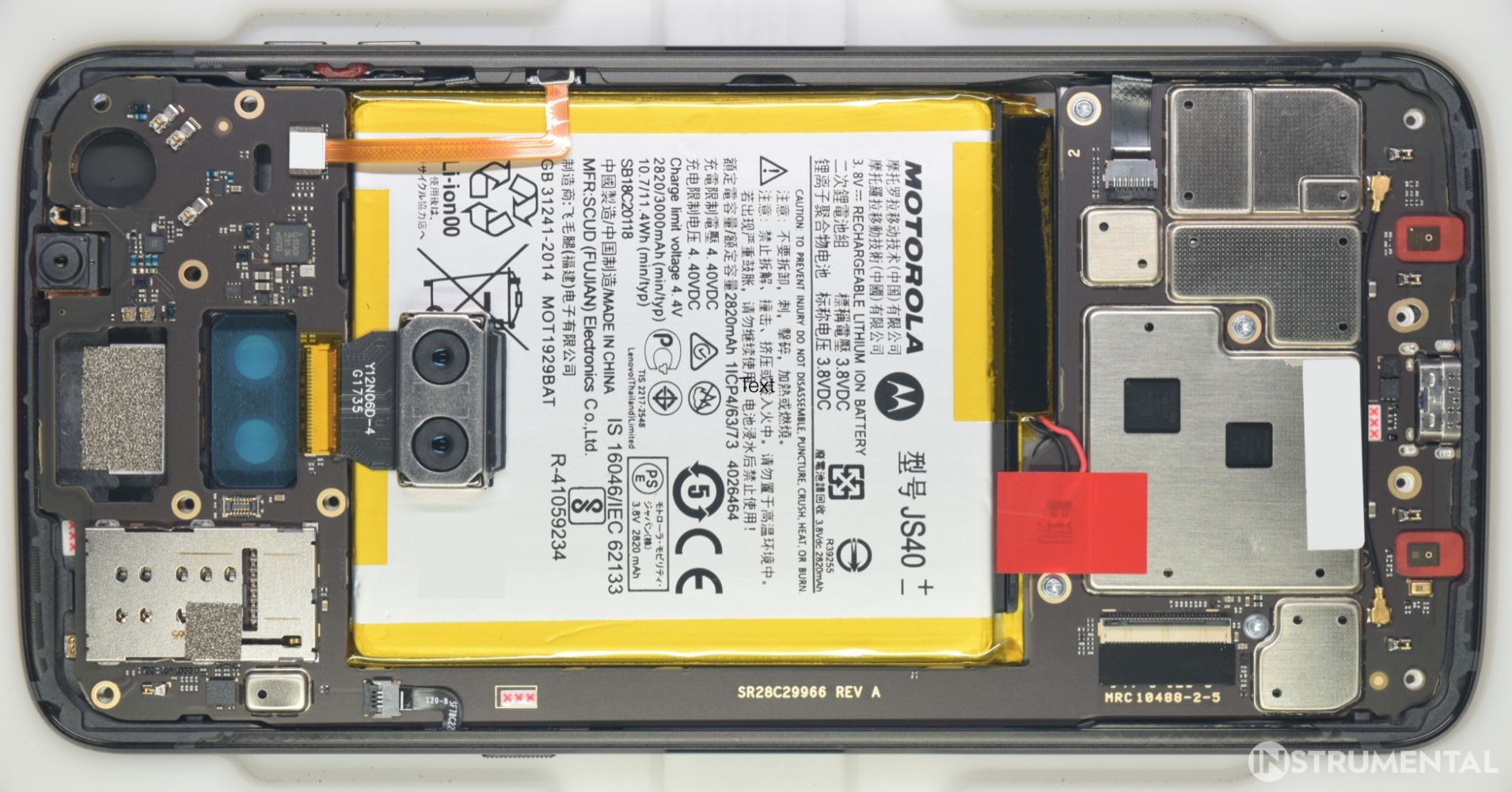
Piccoli problemi che si verificano nelle linee di assemblaggio – per esempio una giuntura che è pochi millimetri più grande di quanto tollerabile, o un componente con un decremento qualitativo – può essere causa di grave imbarazzo per aziende che lavorano nel settore dell’elettronica quando i dispostivi arrivano al pubblico.
Tra i prodotti che hanno avuto problemi in fase di fabbricazione, si segnala il Note 7 di Samsung, con un difetto ad alcune batterie che ha provocato la combustione di vari dispositivi. Anche la produzione del Galaxy Fold è stata fermata dopo che il dispositivo, nelle mani di alcuni giornalisti, ha mostrato problemi associati a impatti a cui sarebbero state sottoposte le aree della cerniera esposte in alto e in basso, ma anche la presenza di sostanze trovate all’interno del dispositivo che hanno contribuito a rompere il display flessibile. Anche Apple pochi giorni addietro ha annunciato un richiamo volontario degli adattatori per prese a muro CA progettati per l’uso principalmente a Hong Kong, Singapore e nel Regno Unito.
“Su Amazon”, spiega Shedletsky, “non mancano prodotti recensiti con una sola stella perché arrivati difettosi al destinatario”. Esperienze di questo tipo possono portare a gravi conseguenze per la vendita dei prodotti e ripercussioni ancora maggiori con gli incontrollabili social media.
Correzioni possono essere applicate nella cosiddetta “fase di sperimentazione progettuale”. In pratica, prima che l’intera struttura cominci ad assemblare ad esempio un telefono, le aziende testano una singola linea produttiva per capire se il procedimento funziona adeguatamente e tutti i pezzi siano assemblati correttamente. Motorola ha usato il sistema di controllo di Instrumental sulla linea produttiva. Fotocamere hanno catturato le immagini dei vari dispositivi prodotti nei vari passaggi nelle linee di assemblaggio, confrontando le foto scattate man mano con immagini di riferimento, controllando l’assenza di elementi, la loro errata disposizione e altri problemi vari.
Il sistema di verifica ideato da Instrumental, sfrutta l’apprendimento automatico e consente di effettuare verifiche visivie di vario tipo per ogni singola unità prodotta, offrendo immediato feedback agli operatori quando viene individuato un problema, riducendo in questo modo i milionari costi di rielaborazione dei processi produttivi.
«Consente di risparmiare denaro in vari modi», spiega Shedletsky. «Il team Motorola ritiene che sia in grado di accelerare quella viene definita “maturità del prodotto”, individuando in anticipo i problemi e consentendo di risolverli con veri ingegneri, non con gomma da masticare e nastro adesivo» (rattoppando alle meglio quanto possibile, ndr).
Instrumental ha racimolato 10 milioni di dollari da soggetti che operano nel Venture Capital e ha 26 dipendenti negli Stati Uniti e in Cina. Ora è alla ricerca di nuovi fondi per migliorare le funzionalità di machine learning come strumento core per ridurre l’apporto umano ancora richiesto nei processi produttivi. Uno dei competitor di Instrumental, si chiama “Landing AI”, azienda fondata da Andrew Ng, pionieri dell’apprendimento automatico che ha un contratto con Foxconn, principale produttore a contratto di Apple. In un post del 2017 su Medium, Ng riferiva già di come l’integrazione dell’intelligenza artificiale nei processi produttivi avrebbe portato a una nuova generazione di prodotti, dispositivi ed esperienze.
Tra gli scogli di queste tecnologie, la potenzialità per i concorrenti di conoscere problematiche in fase di produzione che potrebbero finire nelle mani dei concorrenti. Non mancano tuttavia i modi per cautelarsi anche da queste eventualità.